GET ADVICE
The selection of RPE will usually require expert help.
Please get Intouch with the team at Bay Safety before purchasing any respiratory items.
If not recommend by Bay Safety we waive all liability to the use of the product and any consequences that may arise from the use of incorrect product.
But as an example, general construction work, asbestos work, spraying, brushing/rolling and welding/fabrication working will all require different types or respirator.
General construction work might include cutting, sawing, sanding, drilling, sweeping etc.
This type of work could create silica dust, wood dust and general nuisance dust.
A disposable respirator is usually suitable for most general construction tasks where exposures are low (less than 10 times the workplace exposure standard) and where it will only be used for short periods. Get an expert to help you determine your workplace exposure standards. But for general construction work where the work is more than 50 times the workplace exposure standard, then a full face reusable respirator and filter will be required. Disposable respirators are not suitable for asbestos, spraying, brushing/rolling or welding or fabrication work.
Absorbent gas/vapour cartridges on reusable masks can also be combined with particulate prefilters. The higher the level of risk, the higher the protection should be.
WHAT STANDARDS SHOULD RESPIRATORY PROTECTION MEET?

All our respiratory protectors are tested and certified to meet AS/NZS1716:2012: Respiratory Protective Devices.
This Standard sets out the specific requirements for respiratory protection to protect the user against respiratory hazards in the workplace. Look for the symbols to the left, which indicate the product has been passed by an approved testing agency.
CHOOSING THE CORRECT FILTER FOR PARTICULATE HAZARDS
All our respiratory protectors are tested and certified to meet AS/NZS1716:2012: Respiratory Protective Devices.
This Standard sets out the specific requirements for respiratory protection to protect the user against respiratory hazards in the workplace. Look for the symbols to the left, which indicate the product has been passed by an approved testing agency.
The AS/NZS1716 classification system rates respirator filters for
particulate hazards into three classes:

P1 (for particles generated by mechanical processes, eg grinding, sanding, mining), P2 (for particles generated by mechanical and thermal processes, eg welding, metallic fumes and P3 (for highly toxic particles, eg organophosphate insecticides, radionuclides [the filter is required to be used with a full facepiece]).
The AS/NZS1716 standard also provides a rating system for gas and vapour cartridge filters according to the gas/vapour hazard, and according to the cartridge’s absorption capacity.
A GUIDE TO THE AS/NZS1716 CLASSIFICATION SYSTEM FOR GAS AND VAPOUR CARTRIDGE FILTERS
CLASSIFICATION
|
EFFECTIVE AGAINST
|
TYPICAL USES
|
---|---|---|
P1
|
Suitable for relatively large particles (>1 micron) generated by mechanical processes, eg. grinding, sanding, drilling, sawing, mining. Filters at least 80% of airborne particles.
|
General, not highly hazardous, dust from timber, MDF, masonry, plasterboard, concrete, plaster, brick, stone, painted surfaces; roof and tile dust, metallic dusts; glass, rock wool & mineral wool fibres, large paint particles, pollen, hay, feathers, animal feed dust, spores
|
P2
|
In addition to the above, particles generated by mechanical and thermal processes. This class of filters has a higher capture efficiency to deal effectively with smaller, thermally generated particles like sub-micron sized welding fumes or fertiliser. P2 filters can also capture biologically active airborne particles under specified conditions and are recommended for specific infection control applications (e.g. SARS, TB or other infectious diseases). Filters at least 94% of airborne particles.
|
Fine dust, higher concentrations of dust, welding and metal fumes; low level non-restricted asbestos work, low level water & oil based mists
|
P3
|
In addition to the above, highly toxic particles, eg. organophosphate insecticides, radionuclides, asbestos (the filter is required to be used with a full facepiece). Filters at least 99.95% of airborne particles.
|
For use with toxic materials and/or when very high protection levels are needed
|
PARTICULATE FILTERS SHOULD BE REPLACED WHEN THE FILTER BECOMES DIRTY, TORN OR CLOGGED (IF THE USER CANNOT BREATHE EASILY THROUGH THE FILTER)
|
CHOOSING THE CORRECT ABSORPTION CARTRIDGE FOR GAS/VAPOUR HAZARDS
A GUIDE TO THE AS/NZS1716 CLASSIFICATION SYSTEM FOR GAS AND VAPOUR CARTRIDGE FILTERS
CLASSIFICATION
|
AS/NZS COLOUR CODING
|
EFFECTIVE AGAINST
|
---|---|---|
A
|
Brown
|
Organic vapours, boiling point > 65°C (eg. hydrocarbon or alcohol vapours from paint, solvents, fuel, adhesives)
|
B
|
Grey
|
Inorganic gases (eg. carbon monoxide, chlorine, sulphur dioxide)
|
E
|
|
Acid gases and vapours (eg. sulphuric acid, sulphur dioxide, hydrogen chloride, hydrogen sulphide)
|
K
|
Green
|
Ammonia, methylamine
|
ABEK
|
Brown/Grey/Yellow/Green
|
Combination gases (all of the above)
|
Hg
|
Red
|
Mercury
|
ABSORPTION CAPACITY
|
Effective against
|
|
1
|
Low to medium absorption capacity. Maximum gas/vapour concentration 1,000 ppm.
|
|
2
|
Medium absorption capacity. Max gas/vapour concentration 5,000 ppm.
|
|
3
|
High absorption capacity.
|
WHAT ABOUT WORKING WITH ASBESTOS?
In New Zealand, if you are not a licensed asbestos removalist you are only legally allowed to carry out limited work involving asbestos.
A tradesman or homeowner may remove up to 10m2 of non-friable asbestos or asbestos containing materials (ACM) over the course of a project. ‘Non-friable’ means asbestos that is not in a powder or cannot be crumbled, pulverised, or reduced to a powder by hand pressure when dry. (Example are asbestos cement board (‘Fibrolite’) in good condition or vinyl asbestos floor tiles.)
For this work a P2 mask is the minimum protection level. Licensed workers must use specialised respiratory gear with supplied air.
More information is available in the links at the bottom of this page.
AND OTHER SPECIFIC RISKS LIKE TRICLOROETHANE OR LEGIONNAIRES DISEASE?
Some chemical or biological agents can be very hazardous and require specialised handling, beyond the scope of general advice here.
Worksafe’s recent publication Workplace Exposure Standards and Biological Exposure Indices gives advice on acceptable limits for exposure to a large range of organic, inorganic and biological hazards.
Legionnaires’ disease is another workplace respiratory risk factor. It affects over 100 New Zealanders annually, many of whom encounter the bacteria through working with soil, compost or potting mix. Worksafe recommends using well-fitting P2 masks for protection of at-risk workers, together with other protection measures.
WHEN SHOULD I CHANGE MY DISPOSABLE MASK?
Disposable masks provide convenient, comfortable protection against general respiratory hazards but they are not intended to be used in highly hazardous environments.
In their designed usage they can be expected to last for a maximum of an eight-hour shift; however, in hot, dusty, humid conditions, or where the wearer is removing or adjusting the mask frequently, the effective life of the mask will be much reduced. REPLACE THE RESPIRATOR WITH A NEW ONE IF:
- The respirator is removed in a contaminated area;
- Excessive clogging of the respirator causes breathing difficulty;
- The respirator becomes damaged;
A mask should fit snugly for the entire shift. If not, the mask should be replaced and the old one disposed of.
WHY CHOOSE AN EXHALATION VALVE?
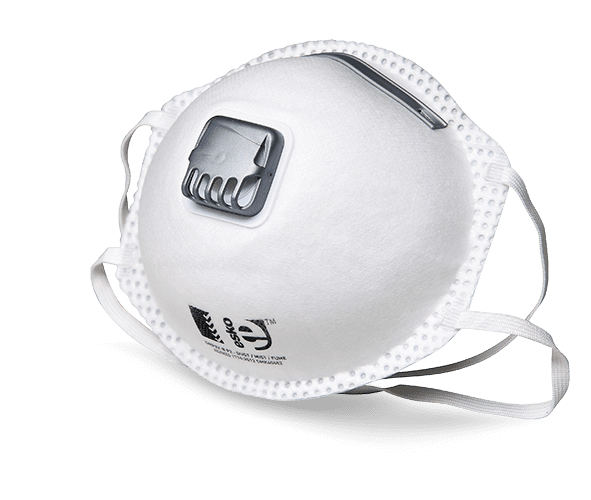
An efficient exhalation valve makes breathing easier and minimises heat and moisture build up, particularly in hot and humid conditions.
WHY ACTIVATED CARBON?
Layers of activated carbon incorporated in ESKO PC531 and PC823 Welding Speciality Respirators are designed to offer relief from the irritation of low levels of ozone, fumes, nuisance odours and vapours especially from paint or welding.
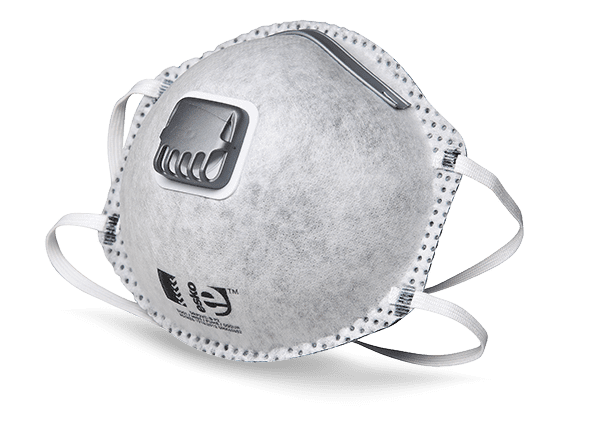
HOW LONG WILL A GAS/VAPOUR CARTRIDGE LAST?
The expected service life of any gas and vapour cartridge is affected by factors including contaminant concentration, the breathing rate of the user, the humidity level, temperature, desorption and storage conditions. Kept in their original sealed wrappers cartridges will last two years from date of manufacture.
Gas and vapour cartridges use activated carbon absorbent material to absorb molecules of contaminant gases. When the absorbent capacity of the cartridge is exceeded the user will usually notice gases or vapours coming through the cartridge. This is called the ‘breakthrough time’.
In use, cartridges should be replaced:
- In accordance with the company’s change schedule,
- After the cartridge’s expiration date,
- At least after six months service, according to the AS/NZS recommendation,
- At any time if contaminant can be smelled or tasted inside the mask or if any irritation is detected.
A safety factor should be applied to ensure that the breakthrough time of cartridges is not exceeded—note that some gases do not have an odour and cannot be detected by smell. If the contaminant is hazardous at low concentrations the worker may already have been exposed to harmful levels by the time any odour is detected.
Assess the factors applying to your particular application and develop a documented schedule for replacing cartridges. Record the date cartridges are put into service and their required replacement date, note this in writing on the cartridge. Adjust the schedule if usage factors change or if the breakthrough time of cartridges is being exceeded.
THE IMPORTANCE OF CLEAN AIR
We hardly ever think about having to breathe. It’s so important to life that the process happens automatically. But because it happens subconsciously it’s easy to underestimate just how important respiratory protection is.
The typical adult takes around 20,000 breaths in a day, which means about 11 cubic metres of air pass through your lungs each day. Imagine the effect on the body if that air is even slightly dirty.
When you breathe in, air passes into the trachea (windpipe). The trachea divides into bronchial tubes that supply the lungs and these divide further into narrower and narrower branches. The smallest airways end in tiny spongy air sacs called alveoli, of which your lungs have over 300 million.
The alveoli are closely surrounded by tiny blood vessels called capillaries. Here the lung carries out its work of exchanging carbon dioxide and oxygenating the blood. The total surface area of the alveoli is amazingly large, estimates vary from 50 to 75 square metres, or roughly the same area as one side of a tennis court.
Dirty air can trigger asthma and respiratory illness. It creates a risk factor for developing lung diseases and provokes development or progression of chronic illnesses including lung cancer, chronic obstructive pulmonary disease (COPD), and emphysema.
When dirty air is breathed in, air pollutants (dust, soot, smoke, chemical toxins) are drawn deep into the lungs. If the pollutant is a dust or mist the particle can lodge in the lungs, in some cases, as with forms of asbestos, permanently. If the pollutant is a toxic gas or vapour it can be transferred through the lung into the bloodstream, where can damage the brain or internal organs.
MORE INFORMATION:
This information is provided as general advice and is not intended to apply to severe hazards such as highly toxic chemicals, isocyanates, radionuclides, asbestos, or in oxygen deficient atmospheres. Specific situations, concentrations and toxicity of hazards can vary greatly. For advice with particular chemical hazards, refer to the manufacturer’s Safety Data Sheets (SDS). For other helpful information refer to:
Worksafe NZ’s webpage Respiratory Protective Equipment—advice for businesses
Information specific to dealing with asbestos hazards—Worksafe guides:
RELEVANT STANDARDS
- AS/NZS 1715:1994: Selection, Use and Maintenance of Respiratory Protective Devices
- AS/NZS 1716:2012: Respiratory Protective Devices